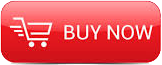
× CAMWorks 2023 SP1 for Solid Edge Close
CAMWorks 2023 SP1 for Solid Edge | 1.5 Gb
Languages Supported: 中文 Simplified, 中文 Traditional, Français, Deutsch, Italiano,
日本語, Polski, Português-Brazilian, Русский, Español, Türkçe, 한국어, Čeština
The HCLSoftware development team is pleased to announce the availability of HCL CAMWorks 2023 SP1. New release gives you the ability to program smarter and machine faster.
CAMWorks for Solid Edge 2023 SP1 what's new
Resolved CPRs 1. CW-120719 CSR-22926 Translation In CAMWorks For Solid Edge 2022 SP3 and 2023 versions,the options to install the Italian and Chinese Traditional languages are missing.
2. CWR-2106 CSR-22037 Toolpath For the specific Mill part, when generating Area Clearance toolpath using ‘Advanced’ method with the ‘Mach deviation’ and ‘Line move deviation’ parameters set to 0.1mm and 0.05mm respectively., it is observed that the toolpath that gets generated is very rough with a lot of long linear moves. This results in poor machining of the part.
3. CWR-2105 CSR-22086 Toolpath For the specific Mill part having multiple Contain Areas, when the Area Clearance toolpath is generated using ‘Advanced’ method with the retract method set to ‘Skim’, the generated toolpath gouges the Center Boss feature’s geometry when retracting between the contain areas. With ‘Previous’ method, the toolpath gets generated correctly.
4. CWR-2093 CSR-21877 Toolpath For the specific 3 Axis Mill part programmed using CAMWorks For Solid Edge, the incorrect Rapid Move to LeadIn arc causes the Z-Level toolpath to gouge the part.
5. CWR-2074 CSR-21355 Toolpath When the 3 Axis Mill Toolpath generation method is set to ‘Advanced’ and a Z Level toolpath is generated when the depth parameter method is set to ‘Scallop’, it makes an incorrect move on the top edge of the fillet corner of the multisurface feature.
6. CWR-2071 CSR-21301 Toolpath For the specific Assembly file, when the 3 Axis Mill Toolpath generation method is set to ‘Advanced’ and user attempts to generate a Pattern Project toolpath for the Pattern Project operation, ‘Error 105’ gets displayed and toolpath fails to generate.
7. CWR-2067 CSR-21227 Toolpath When the 3 Axis Mill Toolpath generation method is set to ‘Advanced’ and a Z Level toolpath is generated for the specific part, it is observed that selecting a point as a Start hint only works on the first Z level. The subsequent levels start at a position that removes the LeadIn moves and plunges the tool into the material.
8. CWR-2066 CSR-21227 Toolpath When the 3 Axis Mill Toolpath generation method is set to ‘Advanced’ and the toolpath is generated for any part having too large LeadIn/ LeadOut moves that may gouge the part, it is observed that the LeadIn/ LeadOut moves get auto removed without any error message being displayed to the user. This results in a Plunge move that damages the part and breaks the tool.
9. CWR-2061 CSR-20980 Toolpath When Contain Area is applied to the Z level toolpath generated for the specific multisurface feature with vertical wall box type shape, the toolpath ignores the bottom flat surface and toolpath also machines up to the stock, which is incorrect.
10. CWR-2052 CSR-20661 Toolpath For the specific Mill part, when the Z Level toolpath (withDovetail shaped user defined tool assigned) is generated using the ‘Advanced’ method, it is observed that the correct LeadIn move is not generated on an identical draft surface feature.
11. CWR-2051 CSR-20660 Toolpath For the specific Mill part, when the Z Level toolpath (with Lollipop tool assigned) is generated using the ‘Advanced’ method, it is observed that the toolpath is making a single vertical move in the entry of a Z depth except the horizontal LeadIn. This is not observed in the other Z depthof cut entry move.
12. CWR-2042 CSR-20504 Toolpath When the 3 Axis Mill Toolpath generation method is set to ‘Advanced’ and an Area Clearance toolpath is generated for any Assembly, there are multiple unnecessary entry moves observed within the same cut level. This happens when the ‘Adaptive Stepdown’ option is checked.
13. CWR-2041 CSR-20432 Toolpath When the 3 Axis Mill Toolpath generation method is set to ‘Advanced’ and a Z Level toolpath is generated for the specific Mill part, the generated toolpath ignores the Z level limits.
14. CWR-1933 CSR-16567 Toolpath When the 3 Axis Mill Toolpath generation method is set to ‘Advanced’ and a Z Level toolpath is generated for the specific Assembly, then it is observed that the toolpath’s LeadIn and LeadOut movement is missing for the two lower levels of the assembly. When regenerating the toolpath after unchecking the ‘Contact Area Only’ option in Z level tab, the Error 105 message gets displayed.
15. CW-120317 CSR-22762 Feeds & Speeds In Feed Speed Library, for Tapping operations, it is not possible to assign a Thread Pitch value of less than 1mm and save those changes without corrupting the data assigned to other parameters.
16. CW-119680 CSR-22512 Post A comment needs to be added in the post libraries (PROBE.LIB, MILL.LIB, MILLTURN_PROBE.LIB) mentioning the list of Probe Cycles which are available in the post but not supported for CAMWorks For Solid Edge 2023 version or previous versions.
17. CW-119473 CSR-22502 Help In UPG Help documentation, the details mentioned for the PROBE_CLEARANCE post variable needs to be updated.
18. CW-119388 CSR-22505 Post When post processing a part model that has Probe operations, the posted code generated fails to populate some of the Probe System variables with correct integer values.
19. CW-119192 CSR-22562 Operations In Assembly mode, for the specific Assembly file, when attempting to save the changes after sorting operations, an error message "Problem in Saving CAMWorks entities to file" gets displayed.
20. CW-119120 CSR-22506 Post Some of the new Probe Systems Variables introduced in Universal Post Generator are not added in the EC Editor LexLib.LXL file and therefore cannot be defined when using EC Editor Lexer.
21. CW-118959 CSR-22425 Post In Universal Post Generator, the default Master.ATR has two variables defined with the same ATTRID (attribute identity).
22. CW-118913 CSR-22374 System When the specific part saved on a shared location or the server is opened using CAMWorks For Solid Edge 2023,when user navigates to the Operation tree and attempts to double click on any Operation node to view Operation Parameters, CAMWorks For Solid Edge crashes.
23. CW-118493 CSR-22348 TechDB In non-English versions of TechDB, if the TechDB window size is reduced from default max size to a smaller size, then in the "Multi stepped holes" page available in Milling menu, it results in overlapping of Copy, Delete, Move Up and Move Down buttons. This makes it very difficult for users to use these buttons.
24. CW-118458 CSR-22307 UIF In Polish version of CAMWorks For Solid Edge, under the F/S tab of Operation Parameters dialog box, it is observed that the text strings in this user interface overlap making it difficult for users to comprehend the displayed text.
25. CW-118371 CSR-22260 API The API ‘MillOperation.OpernType’ returns incorrect value.
26. CW-118222 CSR-22167 UIF In Turn mode, the Center Drill tool is displayed incorrectly within the Preview Window under Center Drill Tool tab of Operation Parameters dialog box.
27. CW-118168 CSR-9362 Toolpath For any Mill part having Pocket feature with chamfer, if the Contour Mill toolpath is generated with side finish pass at a single depth and if LeadIn/ LeadOut has some overlap, then unwanted circular moves get generated in the toolpath. These moves gouge the part.
28. CW-118167 CSR-12177 Toolpath For the specific Mill part, when generating Contour Mill toolpath for Obround Pocket feature, the generated toolpath has an arc move that gouges the part.
29. CW-118045 CSR-9175 Toolpath For the specific Assembly, when generating toolpath for Thread Milling operation where ‘Previous Allowance’ parameter is used, an incorrect toolpath gets generated. When ‘Previous Allowance’ is not used, then the toolpath is correct.
30. CW-117996 CSR-22041 Toolpath For the specific Assembly file, a Contour Mill toolpath having 'Spiral' pattern has been generated for pocket feature. It is observed that portions of the toolpath meant for machining the sidewall of the feature go missing when the bottom finish option "Bottom First" is made active.
31. CW-117987 CSR-22061 UIF For the specific Assembly file, the color for the Leadin and Entry move is getting displayed for the entire Contour Mill toolpath instead of the color assigned in CAMWorks For Solid Edge Display settings. This occurs when Ramp Cut Amount Method is used for the Contour Mill operation.
32. CW-117986 CSR-22025 Toolpath For group features, the Retract moves do not get created for the last feature machined by the toolpath when the "Optimize between groups" option is checked with the ‘Use Skim Plane’ with the Clearance Plane under NC tab.
33. CW-117936 CSR-21972 UIF Under the Posting tab of Machine dialog box, the ‘Probe Type’ scroll button is not visible after the addition of the Probe Options group box.
34. CW-117931 CSR-21956 Setup Sheet When Tooling data is generated for Setup Sheets, it is observed that Flute Length for user-defined tools does not get output.
35. CW-117823 CSR-21923 Feeds & Speeds Attempt by customer to import customized 32-Bit Feeds and Speeds Library into 64 Bit Material Library.exe (in SQLite format) is unsuccessful.
36. CW-117779 CSR-16471 VoluMill For the specific part, the VoluMill Area Clearance toolpath is not considering the stock portion (Undercut Geometry) when the Rest Machining method is set by STL file which also happens to be the stock.
37. CW-117701 CSR-21796 Feeds & Speeds In Material Library, when editing the Feeds and Speeds for Tapping Operations, issues are observed with assigning pitch numbers if they are set to below ‘1’. Observed for Metric units only.
38. CW-117682 CSR-21735 Post When the 4 Axis Mill module is active in CAMWorks For Solid Edge 2022 version, if any 4 Axis Simultaneous operation is generated and user attempts to post process this 4 Axis Simultaneous operation using the 5 Axis Post Processor, then CAMWorks For Solid Edge fails to generate the output. An "Error 5008" message gets displayed.
39. CW-117527 CSR-21770 License When only the Online Activation license is active, and theLicense Manager application is opened in non-admin mode, the License Setup tab and Authorized Modules tab of its UI do not get displayed at all.
40. CW-117526 CSR-21771 License When loading CAMWorks For Solid Edge without an active license, a dialog box that provides users to activate File based license, a Floating Network license, or an Activation ID based license gets displayed. If the Activation ID option is selected, then a message prompting to open the application in Admin Mode gets displayed.
41. CW-117525 –- License When loading CAMWorks For Solid Edge, if there is no active license, then the option/command for Activating License is not available CAMWorks For Solid Edge 2022 menu or Command Manager.
42. CW-117524 CSR-21773 License After loading CAMWorks For Solid Edge 2022 in Demo Mode, when the license is activated using the Activation IDs based on Online License Activation method, CAMWorks For Solid Edge fails to detect the activated license. The ‘License not detected’ message gets displayed.
43. CW-117492 CSR-21696 VoluMill For the specific part file, the VoluMill toolpath generated is exceeding the user-assigned max stepover resulting in the breakage of the tool.
44. CW-117482 CSR-21717 License When the Floating Network license for CAMWorks For Solid Edge license is activated using the Online License Activation Method, the CAMWorks For Solid Edge License Server fails to activate the licensed modules. Not a single one gets activated.
45. CW-117481 CSR-21697 License For the specific customer’s computer systems, the two Standalone CAMWorks For Solid Edge License modulesprocured and activated using the Activation IDs fail to activate. An error message ‘There is no activated product on this machine’ gets displayed.
46. CW-117415 CSR-21654 License The CAMWorks For Solid Edge Floating Network License procured and activated for the specific customer using an Activation ID fails to activate the license.
47. CW-117373 CSR-21623 Toolpath For the specific Assembly, the 2.5 Axis VoluMill toolpath does not get generated when negative allowance is applied. If the allowance is set to zero, the toolpath gets generated correctly.
48. CW-117337 CSR-21617 License If the existing CAMWorks For Solid Edge license that was activated using the License File Based Activation Method expires, then the CAMWorks For Solid Edge License Manager application does not allow the activation of license using the alternative Online license activation method.
49. CW-117317 CSR-21507 Toolpath For the specific Mill part, when 2.5 Axis VoluMill toolpath generated ends up gouging the part.
50. CW-117306 CSR-21578 Rebuild In Assembly Mode, if the active assembly has a common cylindrical stock, then up on executing the Rebuild command, the stock fails to rebuild correctly leading to incorrect calculations and posted NC code.
51. CW-117270 CSR-21522 TechDB When using CAMWorks For Solid Edge linked to a custom TechDB, if the tool from the Tool Library is directly loaded into the Tool tree, the Insert Offset value taken for the holder is incorrect. If Generate Operation Plan command is executed, then correct values are picked.
52. CW-117258 CSR-21515 Toolpath For the specific 2.5 Axis Mill part, when the Feed plane is set to ‘Current Machined Depth’, ‘Distance’ parameter is set to 3mm and the toolpath is generated, then the set parameters are getting applied only for the first loop and missing for all other loops in the toolpath. This results in collision.
53. CW-117108 CSR-21506 TechDB For any part, when using customized TechDB or default TechDB, if a User Defined tool is added to the Tool Crib and the option ‘Use tool crib tools only’ is checked, then CAMWorks For Solid Edge fails to detect the user defined tool present in the tool crib and the operation fails to get generated.
54. CW-117102 CSR-21495 UIF In Polish language user interface of CAMWorks For Solid Edge, the Spin Control button for ‘Final Cut Amount’ underthe Contour Tab is not functional.
55. CW-117079 CSR-21477 Simulation When running simulation for any turn part being machined on a twin-spindle setup, if a series of selections such as keeping the Sub Spindle Chuck highlighted and highlighting last sequence are done. Afterwards, on running the simulation from the beginning, an error in the chuck display is observed.
56. CW-117037 CSR-21448 Simulation When simulation is run for the specific Mill-Turn part having Wrapped features by executing the concerned command from the CAMWorks Ribbon Bar or from CAMWorks NC Manager, gouging of the part is observed. However, if simulation command is executed from individual Mill Setup nodes, then no gouging of the part is observed.
57. CW-116963 CSR-21394 Toolpath In CAMWorks For Solid Edge Operation Tree, the context menu option ‘Optimize between Groups’ does not work. The toolpaths are not optimized within the groups.
58. CW-116947 CSR-21369 Toolpath For any Mill part, when the toolpath compensation is set to ‘Without Compensation’ and the cut depth method is Ramp, the Leadout moves generated for the Contour Mill operation are incorrect.
59. CW-116868 CSR-21348 CSR-22081 License When activating CAMWorks For Solid Edge License using Manual Method of Online Activation, the license request file that needs to be emailed for license activation has a *.cwreq extension. This file extension is confusing as it is identical to the that file extension for License File Based Method of License Activation.
60. CW-116817 CSR-21329 License If the CAMWorks For Solid Edge license has been activated using the Online License Activation method, then the CAMWorks For Solid Edge License Manager does not display the User Subscription Plan (USP) Expiry Date.
61. CW-116796 CSR-21310 Feature For any Mill part having small Curve features, if ‘Extract Machinable Features’ command is executed, then the features do not get recognized correctly and the small curve segments are missed by this command.
62. CW-116754 CSR-21251 API The API ICWTurnNCParam does not return a proper output. It returns as an object and cannot be cast to ICWNCTurnParam.
63. CW-116730 CSR-21232 Toolpath For the specific Mill part, when its 2 Axis Rough Mill operation with Ramp leadin generates a leftover, the succeeding operation using that leftover generatesincorrect toolpath.
64. CW-116477 CSR-21002 UIF In Turn mode, the cursor location for one of the parameters in Cleanup group box present in Groove Rough tab under Operation Parameters dialog box is misplaced.
65. CW-116453 CSR-21006 UIF For the specific Turn part, when clicking on "What's wrong" option in the context menu for any Operation node that has a warning icon, the error message that gets displayed is incorrect.
66. CW-116447 CSR-20914 Operation For any Turn Part, when the Main Spindle coordinates are different from those for the Work Coordinate system, then the operations generated for Sub-Spindle are incorrect.
67. CW-116446 CSR-20979 UIF In the CAMWorks For Solid Edge application linked to usercustomized TechDB, if user attempts to add a user-defined holder and user-defined insert from an assembly file’s component parts using the “Save components of Assembly as Holder/Tool” and saves them to the TechDB, then TechDB ends up saving the entire tool assembly as the insert and holder respectively.
68. CW-116370 CSR-20977 Feeds & Speeds In Material library within the Feeds and Speeds tab, the slider for defining percentage of Default Material and percentage of Base Material must not allow negative values to be assigned.
69. CW-116329 CSR-20947 User Interface When Sorting function available under Tool Crib page on Tool Tab for Operation Parameters dialog box is used, it is observed the graphics window and Preview window display a tool different from the tool selected by the user in the tab.
70. CW-115347 CSR-20229 UIF In Assembly mode, for any operation, when the holder shape is changed from ‘User Defined’ to ‘Basic’, the holder information gets updated, but the corresponding image and the model does not get updated and displays the image meant for user defined holder.
71. CW-115172 CSR-20266 CSR-20326 Setup Sheet In Turn mode, when generating Setup Sheets, if a Groove Rough operation is present, then the variable for Holder edge does not get included in the XML data output. This is observed due to missing API variable.
72. CW-115107 CSR-20285 Toolpath For the specific Mill part, when the Roughing operation generated for its Rectangular Pocket feature has a Spiral Out and a set Min. diameter with the 'Cleanup Pass' active, the generated toolpath has no LeadOut moves.
73. CW-115093 CSR-20263 Toolpath For the specific Mill part having Perimeter Open Pocket feature, when the Pocketing Pattern is set to ‘Offset Roughing’, the toolpath does not maintain uniform stepover on that perimeter open pocket feature.
74. CW-115081 CSR-20254 Toolpath For the specific assembly, the Contour Mill toolpath generated is incorrect and ends up gouging the part on a group feature in the assembly. This happens when the ‘Bottom Finish’ option is enabled for the Contour Mill operation.
75. CW-115039 CSR-20182 Toolpath For the specific Mill part, the VoluMill Rest Machining toolpath generated gouges the part.
76. CW-114966 CSR-20075 Operation For any Assembly operation, when a post operation is added and the Rebuild command is executed, then the newly calculated Total Tool Change Time is incorrectly computed.
77. CW-114928 CSR-20059 Feature For the specific Mill-Turn part, when user attempts to generate a wrap engrave feature using 2D sketches that intersect with the centerline, the feature geometry is partially incorrect resulting in incorrect toolpath.
78. CW-114792 CSR-19962 Feature For the specific Mill part, when Automatic Feature Recognition method is used for extracting machinable 2.5 Axis Mill features, some features get recognized incorrectly.
79. CW-113506 CSR-19351 Toolpath When the specific Assembly that was programmed using CAMWorks For Solid Edge 2019 is opened in CAMWorks For Solid Edge 2022, the VoluMill Rest Machining WIP toolpath generated for its slot feature is gouging the part with its Link moves. This toolpath was working correctly in CAMWorks For Solid Edge 2019.
80. CW-113053 CSR-19122 Setup For the specific Mill-Turn part, whenever the Edit Definition command is executed for the Mill Part Setup and the displayed dialog box is closed; the X-axis of the setup gets rotated by 90 degrees.
81. CW-112974 CSR-19058 TechDB When using CAMWorks For Solid Edge linked to a customized TechDB, the Feature Options for the selected TechDB Operation Parameters are not applied correctly. The user-defined values in the TechDB get applied only tothe first feature. For all other features, the default values get applied.
82. CW-112857 CSR-18917 Mill-Turn For the specific Mill-turn part with ID feature, executing the Generate Operation Plan results in generation of both Straight and Tapered Pipe taps based on programming info present in TechDB while ignoring the Thread tool info assigned by user.
83. CW-112533 CSR-18615 Toolpath For the specific Mill part, the VoluMill toolpath gouges the Slot feature. The toolpath overcuts the target part during entry and retract move at the air segment of the Slot feature.
84. CW-112106 CSR-18530 CSR-20132 API New API required for exposing the CWMillMachine (or CWMachine) for an Assembly document.
85. CW-111344 CSR-17957 UIF For the specific Turn part, the Tool Station Preview dialog box displays the wrong Station IDs when rearranged/sorted.
86. CW-110532 CSR-17555 Toolpath For the specific part, the Rough Mill toolpath with ‘Pocketin’ has Rest machining set to ‘From WIP’. However, this toolpath does not consider the WIP when the cleanup pass is applied. In case of pattern is set to ‘Spiral in’ or ‘Spiral out’ too, applying the cleanup pass results in the "Minimum diameter" value not being considered.
87. CW-109976 CSR-17283 Toolpath For any Contour Mill operation with horizontal passes, when generating the toolpath, the Cutter Compensation codes are not activated in the posted code. This is observed even when the option to use Custom Codes is set to active in the application.
88. CW-109892 CSR-17220 UIF Text with the CAMWorks For Solid Edge Sync Manager user interfaces get cropped if we set the display scale setting to 200%.
89. CW-109345 CSR-16964 Toolpath For the specific Mill part, the Rough and Contour Mill toolpaths fail to get generated for an Irregular U-shaped Slot groove feature/Pocket feature if the groove size is identical to the tool diameter.
90. CW-108241 CSR-16574 Toolpath For the specific Mill part having Chamfers on its Open Pocket feature, the generated toolpath has incorrect LeadIn and LeadOut moves.
91. CW-107502 CSR-16269 VoluMill For the specific Mill part, when generating a VoluMill toolpath for an Irregular Slot feature, an ‘Error -1007’ message gets displayed.
92. CW-106991 CSR-16052 Toolpath For the specific part, when the ‘Stay Down’ function in the Lead-In and Lead-Out for Cut Dept of the Contour Mill toolpath is enabled, the toolpath plunges past the entry point and gouges the part.
93. CW-106676 CSR-15038 Post For the Thread Milling operation, the CUTCOM/ ON command in posted NC code is placed in the wrong location.
94. CW-106296 CSR-15603 Toolpath For any Mill part with a Contour Mill operation with CNC Compensation set to ‘ON’, if LeadIn point is set to "midpoint", LeadIn type is set to "arc" and LeadIn amount is set to "zero", then it is observed that the generated NC Codes contain Cutcom codes. Cutcom codes are supposed to get generated only for linear moves and nor arc moves.
95. CW-106260 CSR-15733 Toolpath For the specific Mill part, the Contour Mill toolpath generated fora Boss feature does not machine the bottom of the part up to the feature depth. This is observed when a Contain area is applied and the Toolpath Center is set to ‘Without Compensation’ while keeping Gouge check option active.
96. CW-106000 CSR-15621 Operation For the specific Mill Assembly, inserting a Post Operation after the Entry Hole operation is not possible.
97. CW-105071 CSR-14648 API The function ‘getFeatureWallFaces’ will not work unless the ‘Rebuild’ command is executed for the active Part or Assembly.
98. CW-104858 CSR-15124 Toolpath When CAMWorks For Solid Edge is linked to a specific customized TechDB; then, it is observed the toolpaths generated for Boss features for any Mill part will have wrong ‘LeadIn’ positions.
99. CW-104678 CSR-14982 Toolpath For the specific Assembly, CAMWorks For Solid Edge fails to generate the toolpath for a Pattern Project operation using ‘flow line between curves’ option.
100. CW-104279 CSR-14729 Feed Speed When CAMWorks For Solid Edge is linked to a customizedTechDB (in Inch mode), then for all 3 Axis Mill operations, the Feedrate value fails to get applied to those operations. In Feed/ Speed tab of Operation Parameters dialog box, the parameter ‘Feed per tooth’ is set to 0 in/min which does not match with the data in TechDB.
101. CW-104106 CSR-14751 Toolpath When generating the toolpath for any Mill part which contains one or more islands on its Face feature, then CAMWorks For Solid Edge fails to consider the island(s), resulting in an incorrect toolpath getting generated.
102. CW-100338 CSR-13262 Feature For the specific Mill part, the features detected using Automatic Feature Recognition are defined with incorrect feature geometry.
× CAMWorks 2023 SP1 for Solid Edge Close
CAMWorks for Solid Edge brings proven, state-of-the-art machining capabilities to Solid Edge users. Since it is accessible directly in the Solid Edge window, CAMWorks for Solid Edge provides a consistent user interface and eliminates time-consuming file transfers. With Geometric's patented Feature Recognition technology running in real-time to capture machined features and automatically generate or update the toolpath, manufacturing-driven design changes can be made to any CAD model using synchronous technology, a unique capability which combines the speed and flexibility of direct modeling with the precise control of dimension driven design. This dramatically streamlines what has traditionally been a time-consuming process. The solution also captures the machining strategy in a customizable database, TechDB, thus allowing efficient machining solutions to be reapplied to future designs with similar features, further enhancing productivity. CAMWorks 2023 combines the benefits of a fully integrated CAD/CAM system with advanced programming technologies such as feature-based programming, automatic feature recognition, knowledge-based machining and TechDB for storing and reusing best practices.
What's new in CAMWorks 2023 - An overview
HCLSoftware is a division of HCL Technologies (HCL) that operates its primary software business. We develop, market, sell, and support over 30 product families in the areas of Customer Experience, Digital Solutions, Secure DevOps, Security & Automation.
Product: CAMWorks
Version: 2023 SP1 build 2023/0421 (21-Apr-2022)
Supported Architectures: x64
Website Home Page : www.camworks.com
Languages Supported: multilanguage
System Requirements: Windows *
Software Prerequisites: pre-installed Solid Edge 2022 or 2023
Size: 1.5 Gb
* System Requirements: × CAMWorks 2023 SP1 for Solid Edge Close
Please visit my blog
Added by 3% of the overall size of the archive of information for the restoration
No mirrors please
× CAMWorks 2023 SP1 for Solid Edge Close
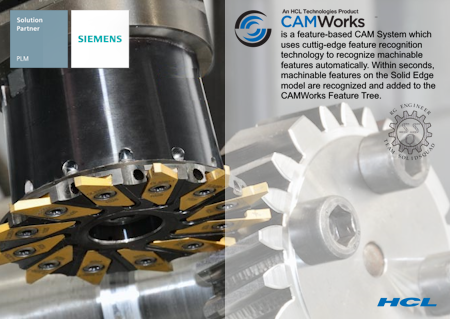
Download File Size:1.49 GB