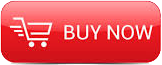
× CAMWorks 2022 SP0 for Solid Edge Close
CAMWorks 2022 SP0 for Solid Edge | 1.9 Gb
Languages Supported: 中文 Simplified, 中文 Traditional, Français, Deutsch, Italiano,
日本語, Polski, Português-Brazilian, Русский, Español, Türkçe, 한국어, Čeština
The GeometricPLM development team is pleased to announce the availability of CAMWorks 2022 SP0 (build 2022/0213) is an intuitive, feature-based CAM software that helps to increase productivity using best-in-class technologies and adaptable automation tools to maximize CNC machining efficiency.
CAMWorks constantly updates its software to satisfy the requirements of the manufacturing industry, as well as offering features to assist manufacturers through its software. A new version of CAMWorks included the following features and enhancements:
Support for barrel tools in milling operations:
The barrel tool has been added to CAMWorks 2022. A parametric shape can be defined for the barrel tool. The tool is frequently used for finishing operations, as it can produce a smoother surface finish. CAMWorks supports five types of barrel tools: standard, conical tangent, tapered, lens, and advanced. Further, barrel tools support multi-axis milling operations, three-axis milling operations, and two-axis milling operations (not supported for centre drills, counter sinks, tapping, thread milling, or VoluMill operations).Tech database allows you to access and modify barrel tools by selecting mill tooling, cutters, and then barrel tools. Next, you can define tool parameters in specific dialogue boxes and save your changes.
Improved user interface for defining and editing multisurface features:
CAMWorks 2022 has updated its user interface to make it easier to define and manipulate the machining of multi-surface features. Geometry tab created under operation parameters allows users to view, add, and modify multisurface features. As well, the automatic contain area feature has been moved to the geometry tab.
Machine to mean for tolerance-based machining:
Using the machine-to-mean function, all dimensions are machined in mean condition and is available on the Run tab in the tolerance-based machining dialog box. This is applicable to milling operations. The part geometry must contain multiple dimensions and several tolerance ranges in order to support this feature.
Conversion of rapid moves to high feed moves for VoluMill toolpaths:
CAMWorks 2022 has introduced check boxes for converting rapid moves into high feed moves in roughing and area clearance operations. A click of the check box initiates the conversion. The feedrate changes automatically. The check box is located in the F/S tab under operation parameters.
Conversion of Arc moves to line moves for VoluMill toolpath:
CAMWorks 2022 has introduced an option for VoluMill which converts Arc moves into number of lines moves. VoluMill provides this feature under its settings. To use it, you must check the checkbox. It is unchecked by default. This will only change the arc move to a line move.
Enhanced toolpath for Contour mill operation:
CAMWorks 2022 has updated the toolpath motion for contour milling. CAMWorks makes sure that the modification maintains the user-defined values for the entry and exit of the tool. The automatic adjustment is determined by the diameter of the tool.
CAMWorks For Solid Edge 2022 SP0 - Resolved CPRs 1. CW-111624 CSR-18140 Machine Simulation In CAMWorks Virtual Machine, incorrect tool shape is displayed if the shank type is set to Neck.
2. CW-111615 CSR-18139 Operation For the specific part, when edit definition is performed on Face Rough operation, then it is observed that the display of the Turn Holder is incorrect.
3. CW-111605 CSR-18120 Post Incorrect value is output for the retract plane of a drill operation generated for a linear pattern of hole features which are at different planes.
4. CW-111595 CSR-18071 Post In Mill-Turn mode, when the toolpath for a pattern of features is posted where the first instance is suppressed then, the posted NC code will include the co-ordinates of the suppressed instance. As the feature instance is suppressed then, the co-ordinates of the suppressed instance should not be post processed.
5. CW-111521 CSR-18083 Post Incorrect values are observed in a posted output for Multi axis mill operation generated on patterned multi surface feature.
6. CW-111514 CSR-17920 API Add API declarations for CWMillMachine.
7. CW-111389 CSR-17973 Operation With the customized TechDB, a crash of CAMWorks For Solid Edge is observed when the user does Save Operation Plan on the features machined in the specific part.
8. CW-111074 CW-110718 CSR-17888 CSR-17727 API Add an API to set the option of selecting ‘Fixture Coordinate system’ under X machining direction in the Mill Part setup parameters.
9. CW-111004 CSR-17852 Post In assembly mode, when output subroutines are set to On then, extra sub programs are posted which is not required.
10. CW-110983 CSR-17654 TechDB A crash of CAMWorks For Solid Edge is seen while opening any part or assembly in inch mode with the specific TechDB.
11. CW-110960 CSR-17808 Rebuild For the specific assembly file, a crash of CAMWorks For Solid Edge is seen when rebuild is performed in the existing CAM data.
12. CW-110945 CSR-17796 Rebuild For the specific assembly file, a crash in CAMWorks For Solid Edge is seen upon performing Rebuild after changing the end condition of multi stepped holes from Through to Blind.
13. CW-110754 CSR-17163 Machine Simulation Add a new header command “USE_COMBINATION_ID_AS_NAME_WHEN_AVAILABLE” to pass the combination id as the tool name to CAMWorks virtual machine.
14. CW-110639 CSR-17686 CSR-17699 CSR-17836 CSR-17615 UIF When the 3 axis Mill toolpaths are regenerated then, the process manager dialog box does not close automatically.
15. CW-110607 CSR-17669 Operation In 3 axis operations, when the option of “Convert to 5 axis” is selected then, the commands of step through, simulation and posting in the CAMWorks For Solid Edge Ribbon Bar get disabled.
16. CW-110600 CSR-17620 Feature For the specific part, when a face feature is created using a sketch then, it is flipped by 180 degrees rendering the feature unusable.
17. CW-110558 CSR-17594 TechDB In TechDB, the user set option for “Use Feed/Speed library for mill” doesn’t affect the Face mill operations.
18. CW-110487 CSR-17549 Operation In Contour Mill operations on combined features, the leadin and lead outs are not same on all features even though the option of apply leadin/outs to all is set to True.
19. CW-110359 CW-99329 CSR-17511 CSR-12948 Feature The part edges identified for chamfering through the option of “Auto select edge for chamfering” should consider the part setup direction so that the toolpath doesn’t gouge the target part.
20. CW-110352 CSR-16946 TechDB In Polish language version of CAMWorks For Solid Edge, when the user defined holder namely “Użytkownika” is saved in TechDB, then the string is replaced with “Uzytkownika” ignoring the second letter (“ż”).
21. CW-110259 CSR-17488 Toolpath For the specific part, the toolpath generated for Rough Mill operation with pattern type set to offset roughing, ignores the user defined avoid area.
22. CW-110065 CSR-17399 CSR-17369 Post When a newly compiled post processor is used to post the Mill toolpath then, the values output for arc moves are incorrect. Instead of outputting the incremental values, the post processor posts the absolute values
23. CW-110047 CSR-17364 UIF When the 3 Axis toolpath generation method is set to Advanced then, then on the rest tab of the operation parameters the controls within the “Boundaries” groupbox should be disabled if the Rest method is not set to ‘Previous Tool’.
24. CW-110036 CSR-17345 Toolpath For the customer specific part, a crash of CAMWorks For Solid Edge is seen upon generating the toolpaths.
25. CW-110002 CSR-17315 Post Add new variables in Universal Post Generator to output values for “CANNED_CYCLE_FIRST_CUT’ and “CANNED_CYCLE_FINAL_CUT’ for turn rough operations.
26. CW-109994 CSR-17314 Post If the post operation is positioned at the end of the operation tree, then upon post processing the codes of the last post operation are incorrectly output.
27. CW-109975 CSR-17152 Machine Simulation Update the machinedef.exe file of the CAMWorks Virtual Machine simulation to support the multi turret machines.
28. CW-109859 CSR-17205 Post Add a new post variable ‘RUNNING_VERSION’ that identifies the version and service pack of the CAMWorks For Solid Edge that is running.
29. CW-109830 CSR-17176 Feed & Speed In Feed and Speed library, for face mill operationparameters the label of “Depth of Cut” should be “Radial depth of cut”.
30. CW-109825 CSR-17154 Help In Universal Post Generator help file, a note stating that ‘OPR_Z_RAPID_PLANE’ variable should not be used for Multiaxis operations needs to be added.
31. CW-109753 CSR-16973 Feed & Speed In CAMWorks Feed and Speed library, if more than one material is imported at the same time then, the data gets corrupted.
32. CW-109734 CSR-17154 UIF In a Multi Axis operation, when the Clearance Plane is defined from a selected point, the UI does not get updatedand incorrect value gets posted in the G code.
33. CW-109651 CSR-17082 Post Incorrect tool numbers are observed in posted output for toolpaths using tools from same station but belonging to different sub stations.
34. CW-109572 CSR-17053 Feed & Speed In the Feed and Speed library, on the bottom left of the Feed and Speed table a handle is observed, when draggedallows to have multiple copies of the table visible which is confusing to the user.
35. CW-109571 CSR-17053 Feed & Speed Remove the unwanted entities from the user interface of CAMWorks feed and speed library which create duplicate columns in the table.
36. CW-109570 CSR-17053 Feed & Speed In the CAMWorks Feed and Speed library, when any row is copied and saved then no notification is displayed regarding the changes.
37. CW-109442 CSR-16917 Feature A crash of CAMWorks For Solid Edge is seen while interactively inserting a hole feature in an assembly file using Solid Edge.
38. CW-109336 CSR-16962 Toolpath For the specific part, incorrect toolpath is generated for Contour Mill operation machining a slot feature having an island with chamfer on the top face.
39. CW-109301 CSR-16983 Translation In Chinese Language version of CAMWorks For Solid Edge, the labels in the VoluMill Settings dialog box are incorrectly translated.
40. CW-109299 CW-106672 CSR-16979 CSR-15869 Machine Simulation If a gang tool is used in a Turn or Mill-Turn machine then, the same is incorrectly displayed in CAMWorks Virtual Machine.
41. CW-109211 CSR-16937 Feature On a Mill-Turn machine the user is not able to assign spindle attribute to a mill feature created after doing a rebuild.
42. CW-109209 CSR-16918 Assembly When specific assembly files saved in earlier version of CAMWorks For Solid Edge are opened in CAMWorks For Solid Edge 2022 then, upon doing a rebuild, a message is displayed indicating that CAMWorks For Solid Edge is unable to recognize features automatically.
43. CW-109184 CSR-16909 UIF Under Additional Probe Parameters, the user can’t add negative values for tolerance parameters.
44. CW-109169 CSR-16878 Feature On Turn machines having dual spindles, when the user edits the dialog for Main spindle co-ordinate system then, the direction of the Sub spindle co-ordinate system gets changed.
45. CW-109159 CSR-16874 Simulation User is not able to simulate the toolpaths generated with tools set as non-center cutting as some of the dimensions result in incorrect tool geometry.
46. CW-109154 CSR-16679 Post Add a new query command “QUERY_FEATURE_NAME” to post.
47. CW-109118 CSR-16831 Toolpath For circular pocket or hole feature, cutter compensation code is not posted for side passes of Contour Mill toolpath when hole center is selected for entry and exit.
48. CW-109068 CSR-16776 CSR16856 Feature For the customer specific part, user is not able to insert a new feature interactively as CAMWorks For Solid Edge becomes unresponsive.
49. CW-109042 CSR-16807 Toolpath For the specific part, the toolpath generated for a Rough Mill operation with pattern type set to Offset roughing does not machine the feature completely.
50. CW-108823 CSR-16353 System With new UPG installed on the system, the user gets an error message as the system fails to trace the installed post folder.
51. CW-108524 CSR-16720 Toolpath For the specific part, the toolpath for a Rough Mill operation with pattern type set to Volumill gouges the feature as the location of the entry hole is incorrect.
52. CW-108488 CSR-16718 Toolpath For the specific part with stock set by using a STL file, the rapid plane, clearance plane and Z start depths of 3 axis toolpath are incorrect.
53. CW-108286 CW-108128 CSR-16609 CSR-17124 CSR-16513 CSR-17077 Feature With Solid Edge 2021, a crash of CAMWorks For Solid Edge is seen whenever the user does rebuild on the existing CAM data.
54. CW-108242 CSR-16578 Toolpath For the specific part, an extra pass gets generated when the existing toolpath of Contour Mill operation is regenerated.
55. CW-108237 CSR-16549 Post If canned cycle is used for Turn threading operation, then incorrect values of X and Z start points are posted in the G code.
56. CW-108069 CSR-16371 Feed & Speed In Feed and Speed library, when ‘Delete Tool Material’ is selected then, ‘Add Tool Material’ dialog box is launched instead of delete tool material dialog box.
57. CW-108056 CSR-16371 Feed & Speed In the German version of Material library, the string ASTM number is incorrectly translated.
58. CW-107814 CW-107813 CSR-16371 Feed & Speed In the 64-bit Feed and Speed library, the delete tool command invokes the dialog for Add new material.
59. CW-107811 CSR-16362 Toolpath For the specific part, the toolpath for a curve project operation cannot be generated
60. CW-107771 CSR-16408 Operation When the toolpath of a Rough Mill operation with pattern type set to Volumill and entry method set to Entry drill is mirrored then, the position of the entry drill is not mirrored accordingly.
61. CW-107491 CSR-16239 Toolpath When the 3 Axis toolpath generation method is set to Advanced then, for the specific part the user is unable to generate toolpath for Z level operation.
62. CW-107378 CSR-16204 Assembly For the specific assembly the user defined FCS from a sketch point is not retained upon closing and reopening the assembly.
63. CW-106941 CSR-16018 TechDB In TechDB, the Mill-Turn tool crib for Turn assembly tools allows to select Mill holder. It should not be active when Turn insert-holder combination is selected.
64. CW-106938 CSR-16003 Simulation For the specific part setting low variable allowances in Turn operations results in incorrect display of simulation and the part appears to be overcut.
65. CW-106933 CSR-106933 Operation In Turn operations the user defined values of Z end in the Turn operation setup are not applied unless the user edits the operations and generates the toolpath again.
66. CW-106809 CSR-10781 Toolpath For the specific part, some of the user defined values for corner rounding are not applied to the Contour Mill toolpath and this results in incorrect toolpath.
67. CW-106672 CSR-15869 Machine Simulation In CAMWorks Virtual Machine, the gang tools set in a MillTurn tool crib are incorrectly positioned.
68. CW-106354 CSR-15800 License Modify the dongle Key Manager program to be able to view COD file so that the resellers can verify the modules included in the COD file.
69. CW-106258 CSR-15751 Operation Upon doing a rebuild on a Mill part, the dimensions of the Face feature are not updated and because of this the corresponding operations of the feature are not updated.
70. CW-106042 CSR-15568 Simulation When Wire EDM is added as an active add-in along with the CAMWorks For Solid Edge add-in then, while simulating the mill toolpaths the flute length of the tool is not displayed.
71. CW-105995 CSR-15606 Toolpath For the specific assembly, the orientation of the Mill part setup gets changed to an incorrect direction when the corresponding feature setup is edited.
72. CW-105399 CSR-15264 Toolpath For the specific assembly file, the toolpath generated for Contour Mill operation with toolpath center set to with compensation on a curve feature doesn’t generate any cut moves.
73. CW-105348 CSR-15297 Simulation Incorrect results are seen when a Contour Mill toolpath with toolpath center set to without compensation is simulated.
74. CW-105184 CSR-15220 Feed & Speed In CAMWorks Feeds and Speeds library, the resized dialogs are not retained upon restarting the application.
75. CW-105104 CSR-15186 Operation User should not be able to select STL files to define the user defined Mill holder.
76. CW-104634 CSR-15045 Operation The time taken to open the “Operation Parameter” dialog box is significantly more when the tool crib contains more number tools even though they are not assigned to any operation.
77. CW-104621 CSR-15004 Toolpath For the specific part, the turn toolpaths display an incorrect warning message saying that the toolpath is not computed because of a collision
78. CW-104154 CSR-14796 Toolpath The toolpath of a Rough mill operation with pattern type set to Volumill doesn’t consider the multiple avoid areas defined using a single sketch and instead considers only a single closed contour.
79. CW-103903 CSR-14710 Rebuild For an Assembly file, when the Fixture Coordinate System is defined using the part vertex and when the part is shifted by changing the distance, it is observed that the Fixture Coordinate System does not get updated with respect to part.
80. CW-102460 CSR-14072 TechDB The value set for the spiral ramp angle of a Volumill toolpath is not written to corresponding TechDB field when Save Operation Plan is done on the feature in CAMWorks For Solid Edge.
81. CW-102394 CW-99329 CW-94636 CSR-14049 CSR-12948 Feature In some specific parts, the time taken to identify curve features for chamfering is significantly high and, unwanted edges are selected as curve features.
82. CW-102325 CSR-13957 Toolpath For the specific assembly, the toolpath for Rough Mill operation ignores the defined fixtures and collides with the fixture bodies.
83. CW-100896 CSR-13390 Operation When Mill Part setup is manually inserted then, it does not calculate correct rotary and tilt axis under indexing tab of mill part setup if machine is saved with predefined rotary or tilt direction in TechDB.
84. CW-100891 CSR-13308 Feeds & Speed In Feed and Speeds library the “Axial depth of cut” optionremains disabled unless dialog is refreshed toggling with another operation type.
85. CW-99223 CSR-12909 Simulation For the specific part, the stock defined using an extruded sketch is not being set correctly in simulation.
86. CW-99164 CSR-12871 Toolpath For the specific part, the toolpath is not generated for Face mill operation.
87. CW-98683 CSR-12602 UIF The tool description in the operation name when using a user defined tool is incorrect.
88. CW-97991 CSR-12174 Toolpath For the specific part, incorrect toolpath is generated for a Turn Rough operation.
89. CW-97821 CSR-12111 CSR-12637 Simulation For the specific assemblies, in simulation the tool makes unwanted moves in space which are not present in the toolpath generated for the features.
90. CW-95796 CSR-11240 Toolpath For the specific assembly, the toolpath for rough mill operation with pattern type set to Offset roughing gouges the parts defined as fixtures.
91. CW-95792 CSR-11157 Feature For the specific assembly, incorrect depth of the perimeter feature is calculated when the features are recognized through Extract Machinable Feature command.
92. CW-92580 CSR-17795 Machine Simulation The letters used to define the path of CAMWorks virtual machine should not be case sensitive.
93. CW-88314 CSR-9682 Toolpath For the specific part, incomplete toolpath is generated for the Rough Mill operation on an open pocket feature having islands.
94. CW-85059 CSR-7534 Feature For the specific assembly, the depth of the part perimeter feature becomes incorrect after a rebuild.
95. CWR-1986 CSR-18004 Toolpath When the 3 Axis toolpath generation method is set to Advanced then, for the specific part, the toolpath for the Z level operation with rest machining results in error and no toolpath is generated.
96. CWR-1985 CSR-17968 Toolpath When the 3 Axis toolpath generation method is set to Advanced then, for the specific part the toolpath generated for Z level operation does not consider the holder avoidance.
97. CWR-1954 CSR-17296 Toolpath When the 3 Axis toolpath generation method is set to Advanced then, for the specific part the toolpath for the Z level operation gouges the part.
98. CWR-1953 CSR-17300 Toolpath When the 3 Axis toolpath generation method is set to Advanced then, for the specific part incorrect toolpath isgenerated for Flat area operation
99. CWR-1948 CSR-17110 Toolpath When the 3 Axis toolpath generation method is set to Advanced then, for the specific part incorrect toolpath is generated for Flat area operation.
100. CWR-1945 CSR-17098 Toolpath When the 3 Axis toolpath generation method is set to Advanced then, for the specific part the toolpath generated for the Pencil Mill operation displays unwanted moves.
101. CWR-1918 CSR-15866 Toolpath When the 3 Axis toolpath generation method is set to Advanced then, for the specific part the toolpath generated for Z level operation does not adhere to user defined allowances.
102. CWR-1915 CSR-15945 Toolpath When the 3 Axis toolpath generation method is set to Advanced then, for the specific part the toolpath for Z Level operation is not generated.
103. CWR-1910 CSR-15671 Toolpath When the 3 Axis toolpath generation method is set to Advanced then for the specific part incorrect toolpath is generated for the Z level operation as it does not adhere to the user defined values for the slope angle.
104. CWR-1862 CSR-14253 Toolpath When the 3 Axis toolpath generation method is set to Advanced then, for the specific part incorrect toolpath is generated for Z Level operation as the user defined avoid features are ignored
× CAMWorks 2022 SP0 for Solid Edge Close
CAMWorks for Solid Edge brings proven, state-of-the-art machining capabilities to Solid Edge users. Since it is accessible directly in the Solid Edge window, CAMWorks for Solid Edge provides a consistent user interface and eliminates time-consuming file transfers. With Geometric's patented Feature Recognition technology running in real-time to capture machined features and automatically generate or update the toolpath, manufacturing-driven design changes can be made to any CAD model using synchronous technology, a unique capability which combines the speed and flexibility of direct modeling with the precise control of dimension driven design. This dramatically streamlines what has traditionally been a time-consuming process. The solution also captures the machining strategy in a customizable database, TechDB, thus allowing efficient machining solutions to be reapplied to future designs with similar features, further enhancing productivity.
CAMWorks for 2022 provides advanced new features to help you take full advantage of your CNC machines
CAMWorks 2022 Tips & Tricks
GeometricPLM by HCL Technologies a specialist in the domain of engineering solutions, services and technologies. Its portfolio of Global Engineering services, Product Lifecycle Management (PLM) solutions, Embedded System solutions, and Digital Technology solutions enables companies to formulate, implement, and execute global engineering and manufacturing strategies aimed at achieving greater efficiencies in the product realization lifecycle.
On April 1st 2016, Geometric got into an agreement with HCL Technologies to transfer of its business to HCL Tech by way of demerger, except for its 58% share in the joint venture with Dassault Systèmes (3DS) (3DPLM Software Solutions Limited (3DPLM)). The transition has become effective on March 2nd 2017, after seeking all statutory approvals.
Product: CAMWorks
Version: 2022 SP0 (build 2022/0213)
Supported Architectures: x64
Website Home Page : www.camworks.com
Languages Supported: multilanguage
System Requirements: Windows *
Size: 1.9 Gb
* System Requirements: × CAMWorks 2022 SP0 for Solid Edge Close
Please visit my blog
Added by 3% of the overall size of the archive of information for the restoration
No mirrors please
× CAMWorks 2022 SP0 for Solid Edge Close
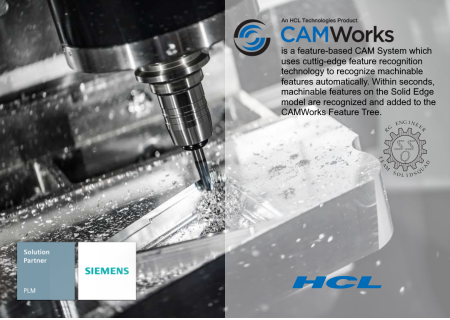
Download File Size:2 GB